為進一步實現高質高效自動化焊接,中國船舶武漢船機工藝研究中心與鋼構制造部緊密配合,結合廠內的CMT焊接機器人開展了海工吊撐桿自動化焊接工藝試驗,為后續(xù)產品提高生產效率,提升產品質量打下基礎。
目前,廠內海工吊機撐桿的焊接主要采用二氧化碳氣保焊焊接,雖能滿足基本要求,但焊接效率不高。相比而言,CMT焊接機器人能同時保證焊接的精確性和安全性。但在焊接過程中,焊接機器人行走軌跡受加工、安裝、焊接變形等因素影響,會與實際行走軌跡要求位置出現一定偏差,導致焊接質量不高。
針對以上問題,工藝研究中心積極展開技術攻關和產品試驗驗證,相關技術員查找資料,調整相關工藝參數。在工字梁結構件自動焊中引入單面焊雙面成型技術,通過單面施焊,在焊件上獲得雙面成型的焊縫,該焊縫的正反面均具有良好的內在及外觀質量,并將該技術在其它產品上得到應用驗證。
該項技術改進,保證了CMT機器人焊接時焊道整齊美觀,外觀質量高,有效減少了因焊接變形導致清根、校正和修磨等工作量,大大提升了生產效率,更好地響應客戶需求。
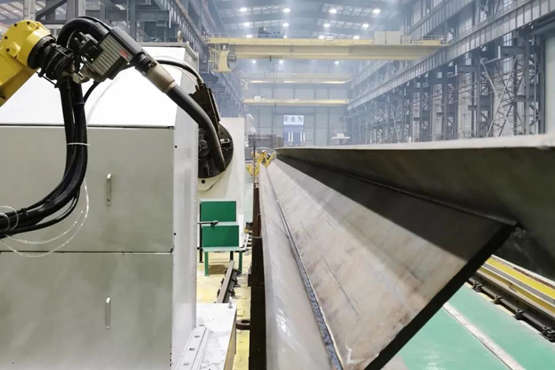
針對以上問題,工藝研究中心積極展開技術攻關和產品試驗驗證,相關技術員查找資料,調整相關工藝參數。在工字梁結構件自動焊中引入單面焊雙面成型技術,通過單面施焊,在焊件上獲得雙面成型的焊縫,該焊縫的正反面均具有良好的內在及外觀質量,并將該技術在其它產品上得到應用驗證。
該項技術改進,保證了CMT機器人焊接時焊道整齊美觀,外觀質量高,有效減少了因焊接變形導致清根、校正和修磨等工作量,大大提升了生產效率,更好地響應客戶需求。