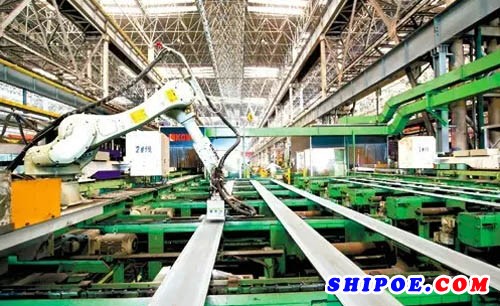
當下,以智能化為特征的新型制造業(yè)正悄然興起。面對新一輪科技革命和產(chǎn)業(yè)變革帶來的機遇和挑戰(zhàn),國務院制定并印發(fā)了《中國制造2025》。這是我國實施制造強國戰(zhàn)略第一個十年行動綱領。
今天的全球市場對航運業(yè)賴以生存的生產(chǎn)工具——船舶提出了更高的要求,必須提供更多、滿足航運企業(yè)運營需求的產(chǎn)品種類,而且產(chǎn)品的生產(chǎn)周期也在日益縮短。這就意味著生產(chǎn)設施必須變得更加靈活,從而能快速地響應市場變化。盡管日本、韓國等先進造船國家已在智能造船領域搶得先機,實際上,以南通中遠川崎船舶工程有限公司為代表的中國造船企業(yè)也已啟動了邁向智能制造的行動。
近年來,歐美等發(fā)達國家提出“再工業(yè)化”戰(zhàn)略,強力推動“制造業(yè)回歸”,以智能制造為代表的高端制造是這些國家實現(xiàn)“再工業(yè)化”的主要手段,并正引領新一輪的工業(yè)革命。他們在智能制造領域采取了一系列的行動和措施,其中包括:德國“工業(yè)4.0”、美國“產(chǎn)業(yè)互聯(lián)網(wǎng)”、日本“機器人新戰(zhàn)略”等。
目前,《中國制造2025》已上升到國家戰(zhàn)略,今年年初,工信部發(fā)布了《2015年智能制造試點示范專項行動實施方案》,明確了未來3年專項行動實施的目標、行動和任務。從我國發(fā)展現(xiàn)實看,加快發(fā)展智能制造任務非常迫切。
智能制造是面向產(chǎn)品全生命周期、實現(xiàn)泛在感知條件下的信息化制造,是在現(xiàn)代傳感技術、網(wǎng)絡技術、自動化技術、擬人化智能技術等先進技術的基礎上,通過智能化的感知、人機交互、決策和執(zhí)行技術,實現(xiàn)設計過程、制造過程和制造裝備智能化,是信息技術和智能技術與裝備制造過程技術的深度融合與集成。
作為我國造船標桿企業(yè),南通中遠川崎船舶工程有限公司緊跟國家宏觀政策步伐,成立20年來,先后前瞻性地完成了散貨船、集裝箱船、油輪三大主流船型及汽車滾裝船、多用途船等多產(chǎn)品的開發(fā)與升級換代,并在相關技術方面領跑中國造船,躋身世界先進行列。
早在2007年,南通中遠川崎船舶工程有限公司便超前謀劃,著手生產(chǎn)、設計的信息化改造,實施信息化和工業(yè)化兩化融合戰(zhàn)略,并在此后獲得“江蘇省兩化融合示范企業(yè)”稱號。2012年開始積極尋求突破,將擴大機器人應用和實施生產(chǎn)線改造等智能制造手段作為信息化和工業(yè)化深度融合的切入點,以大幅降低人工成本、減輕勞動強度、改善作業(yè)環(huán)境、提高生產(chǎn)效率和產(chǎn)品質(zhì)量,從而持續(xù)提升企業(yè)競爭力。目前已建成4條機器人生產(chǎn)線,成為全國樣板。2015年7月,該公司船舶制造智能車間被確定為國家工業(yè)和信息化部智能制造試點示范項目,國內(nèi)造船企業(yè)獨此一家。
中遠造船工業(yè)公司所屬的南通中遠川崎船舶工程有限公司,主要從事中、高端船舶的研發(fā)和建造,產(chǎn)品類型涵蓋各型散貨船、大型集裝箱船、超級油輪、礦砂船、汽車滾裝船等主流船型,以及多用途船、雙燃料船、LNG船等特種船,年生產(chǎn)能力約250萬載重噸。公司成立以來,實現(xiàn)了高起點、跨越式發(fā)展,已建成交付的各種大型遠洋船舶中,30萬噸超級油輪、30萬噸礦石運輸船、13386標箱集裝箱船等7個船型,填補了中國造船業(yè)多項空白。建造工時、鋼材利用率、萬美元產(chǎn)值耗電量、生產(chǎn)效率等主要經(jīng)濟技術指標達到國內(nèi)領先、國際先進水平,先后被認定為“江蘇省船舶技術工程研究中心”、“博士后創(chuàng)新實踐基地”,3次被認定為國家級“高新技術企業(yè)”。
2007年開始,南通中遠川崎公司大規(guī)模利用信息技術改造傳統(tǒng)設計建造手段,升級改造計算機集成制造系統(tǒng)功能,進一步提升信息系統(tǒng)的應用范圍和信息系統(tǒng)集成度,擴大數(shù)字化制造裝備的使用規(guī)模,實現(xiàn)了以信息化和工業(yè)化深度融合為標志的數(shù)字化造船。經(jīng)過幾年的開發(fā)、創(chuàng)新和實踐,建立了完善的計算機集成制造系統(tǒng),將貫穿船舶產(chǎn)品全生命周期的CAD、CAPP、CAM、ERP等高度集成應用,在研發(fā)、設計、采購、制造、財務、管理等流程中實現(xiàn)信息化和數(shù)據(jù)共享,并由此獲得“江蘇省兩化融合示范企業(yè)”稱號。
2012年,南通中遠川崎確立了將智能造船作為轉(zhuǎn)型升級的主攻方向和實現(xiàn)造船強廠的主要途徑,相繼投產(chǎn)4條機器人生產(chǎn)線。通過不斷攻關,初步建立了以數(shù)字化、模型化、自動化、可視化、集成化為特征的智能造船和精益管理體系,真正實現(xiàn)了研發(fā)、設計、生產(chǎn)、管理等環(huán)節(jié)全面融合、協(xié)同運行,已建成具有示范作用的船舶制造智能車間,實現(xiàn)了各加工系列的智能制造,達到工裝自動化、工藝流水化、控制智能化、管理精益化,保障了產(chǎn)品質(zhì)量的穩(wěn)定,縮短了加工周期,極大地提高了生產(chǎn)效率,產(chǎn)品質(zhì)量和建造效率達到世界先進水平。
通信網(wǎng)絡系統(tǒng)覆蓋全廠
作為船舶智能車間的基礎設施建設,南通中遠川崎建立了覆蓋全廠的計算機網(wǎng)絡系統(tǒng),通過光纖連接到各生產(chǎn)車間,并借助計算機網(wǎng)絡,實現(xiàn)物理制造空間與信息空間的無縫對接和映射,為精細化和智能化管控提供基礎。
技術研發(fā)部門通過CAD、CAPP、CAM、虛擬仿真等技術的運用,實現(xiàn)了產(chǎn)品研發(fā)設計的數(shù)字化。利用生產(chǎn)運行數(shù)據(jù)和設計數(shù)據(jù),將現(xiàn)場作業(yè)、運營、管理等固化成各類工藝、業(yè)務模型和規(guī)則,根據(jù)實際需求調(diào)度適用的模型來適應各種生產(chǎn)管理活動的具體需要。
同時,還利用數(shù)字專線連接大連中遠川崎船舶工程有限公司,實現(xiàn)兩家船廠異地協(xié)同設計、協(xié)同采購、協(xié)同經(jīng)營、信息共享。
1.計算機輔助設計(CAD)系統(tǒng)
TRIBON系統(tǒng)在南通中遠川崎公司船、機、電等各專業(yè)領域得到廣泛運用,建立數(shù)字化樣船。包括船體構(gòu)造、管系、主要機器設備等在內(nèi)的所有部件,均在計算機內(nèi)設計完成。通過計算機網(wǎng)絡,可實現(xiàn)多專業(yè)設計人員的并行設計、協(xié)同設計、實時數(shù)據(jù)共享。同時,對計算機輔助設計系統(tǒng)進行了大量的二次開發(fā),使其與設計及制造體系緊密結(jié)合,減少了大量重復作業(yè)和錯誤作業(yè),有效提高了設計、制造的質(zhì)量與效率。
2.計算機輔助工藝設計(CAPP)
該公司開發(fā)的CAPP系統(tǒng),可提取CAD系統(tǒng)中所有的設計數(shù)據(jù),并根據(jù)規(guī)范要求和生產(chǎn)條件進行批量的數(shù)據(jù)加工處理,從而自動生成符合制造加工要求的生產(chǎn)圖面及數(shù)據(jù),同時將與建造工藝相關的焊接收縮量,加工精度和余量等信息標準化或基準化,運用到船舶三維設計模型中。
3.計算機輔助加工(CAM)
利用基于DNC車間管理模式,將制造過程有關的設備(如數(shù)控切割機等)與上層控制計算機集成為一個系統(tǒng),從而實現(xiàn)制造設備與上層計算機之間的信息交換,通過接收CAD和CAPP系統(tǒng)處理完的數(shù)據(jù),并將數(shù)據(jù)傳輸至數(shù)控切割機和機器人設備,實現(xiàn)了從鋼板下料開始到切割成品產(chǎn)出的自動處理。
智能制造系統(tǒng)領先一步
南通中遠川崎在船舶智能制造方面,率開國內(nèi)先河。高度自動化的流水作業(yè)生產(chǎn)線加上柔性化的船舶生產(chǎn)工藝流程,實現(xiàn)了船舶制造的自動化操作和流水式作業(yè)。同時,將反映生產(chǎn)狀態(tài)的各類信息集中和融合,為操作人員提供一個直觀的加工場景,確保準確掌握信息,實現(xiàn)快速作業(yè)。
1.型鋼生產(chǎn)線
型鋼是船體常用部材之一,原先的生產(chǎn)方式,從畫線、寫字到切割、分料,完全采用手工作業(yè),效率低,周期長,勞動強度大,且難免出現(xiàn)誤操作。型鋼自動化生產(chǎn)線建成后,實現(xiàn)了從進料→切割→自動分揀→成材分類疊放全過程的智能制造,包括物料信息傳輸和物料切割智能化以及物料分類感知智能化,有效減少了人工成本,縮短了生產(chǎn)周期,降低了勞動強度,為后續(xù)擴大機器人應用積累了經(jīng)驗。
2.條材機器人生產(chǎn)線
條材是分段制造的主要部材之一,它的特點是數(shù)量多,大部分部材比較短小。原來的生產(chǎn)方式,包括畫線、寫字、開條、端部切割、打磨、分料等全是手工作業(yè),效率低,生產(chǎn)周期長,容易出錯。條材機器人生產(chǎn)線的投產(chǎn),實現(xiàn)了信息傳輸和物料傳輸感知智能化以及加工智能化,提高了生產(chǎn)效率,縮短了生產(chǎn)周期,降低了勞動強度。
3.先行小組立機器人生產(chǎn)線
盡管造船中厚板電弧焊接實現(xiàn)機器人作業(yè)困難很多,但南通中遠川崎還是從最簡單的先行小組材開始,推進機器人焊接。傳統(tǒng)的制造方式中,鋼板在定盤上全面鋪開,一塊一塊地裝配、焊接、翻身、背燒,占用面積大,制造周期長,效率低。先行小組立機器人生產(chǎn)線投產(chǎn)后,實現(xiàn)了工件傳輸和焊接智能化,以及自動背燒、自動工件出料,整條生產(chǎn)線僅配一名員工操作,配員減少一半以上。
流水線生產(chǎn)方式是工業(yè)化大生產(chǎn)的必然要求。對造船業(yè)而言,車間內(nèi)生產(chǎn)作業(yè)的流水線化將是今后實施船舶智能制造的一個重要發(fā)展方向。目前南通中遠川崎已實施了大艙肋骨生產(chǎn)線、Y龍筋生產(chǎn)線、焊接裝置等數(shù)個半自動化生產(chǎn)線技改項目,取得了良好的效果。
4.小組立機器人焊接生產(chǎn)線
全線長84米,包括四臺焊接機器人,以焊接散貨輪N分段為主,較3號先行小組立生產(chǎn)線更為先進。采用三維模擬部材,利用專用KCONG軟件進行自動化生產(chǎn)。四臺機器人能夠單獨焊接,也能互相配合作業(yè),可以針對部材大小,靈活應對各種情況。整條線只需要2—3人就能正常運轉(zhuǎn)。
5.智能物流系統(tǒng)
采用“橫向到邊、縱向到底”的設計原則,建立了功能完善的智能物流系統(tǒng),并與設計系統(tǒng)高度集成,從而將企業(yè)的人力、資金、信息、物料、設備、時間、方法等各方面資源充分調(diào)配和平衡,為企業(yè)加強財務管理、提高資金運營水平、減少庫存、提高生產(chǎn)效率、降低成本等提供強有力的支持。
南通中遠川崎的智能造船模式使設計、制造、加工、管理信息一體化,貫穿了零件設計信息、工藝信息、工裝信息、材料配套信息、加工信息和裝配信息的生成和傳輸全過程,并且在采購申請單、物料清單、托盤清單等業(yè)務方面全面實現(xiàn)了無紙化。
目前,南通中遠川崎已完成三大主流船型及汽車滾裝船、多用途船等產(chǎn)品的升級換代,正在建造的世界首艘大型LNG雙燃料動力汽車滾裝船和將要建造的19000—21000標箱超大型集裝箱船等,在相關技術方面均走在世界前列。據(jù)了解,該公司在未來發(fā)展中還將繼續(xù)擴大工業(yè)機器人應用,以持續(xù)提升企業(yè)市場競爭力。
背景鏈接:南通中遠川崎船舶制造智能車間介紹
■發(fā)展沿革
(1)成立初期至2006年,是南通中遠川崎以建立計算
機集成制造系統(tǒng)為目標的起步階段。這一階段中,建成了覆蓋全廠的計算機局域網(wǎng),信息系統(tǒng)普遍應用于船舶設計與生產(chǎn)工藝設計、物流管理、現(xiàn)場制造等,不過在數(shù)字化制造裝備方面投入不多,只有數(shù)臺數(shù)控切割設備,效率提高不多。
?。?)2007年至2011年,隨著南通中遠川崎二期工程的推進,開始大規(guī)模利用信息技術改造傳統(tǒng)設計建造手段,升級改造了計算機集成制造系統(tǒng)的功能,擴大了信息系統(tǒng)的應用范圍,提高了信息系統(tǒng)集成度,擴大了數(shù)字化制造裝備的使用規(guī)模,實現(xiàn)了CAD/CAE/CAM/CAPP與ERP系統(tǒng)的良好集成,數(shù)控數(shù)據(jù)自動生成后通過光纖自動傳輸?shù)浆F(xiàn)場的數(shù)控切割機設備,實現(xiàn)了以信息化和工業(yè)化深度融合為標志的數(shù)字化造船,并于2012年12月獲得“江蘇省兩化融合示范企業(yè)”稱號。
?。?)近年來,面對持續(xù)低迷的船舶市場和不斷上升的制造成本,南通中遠川崎積極尋求突破,擴大機器人應用和實施生產(chǎn)線改造等智能制造手段,大幅度減少人工成本、減輕勞動強度、改善作業(yè)環(huán)境、提高生產(chǎn)效率、降低產(chǎn)品不良品率,從而持續(xù)提升企業(yè)競爭能力。2012年起,南通中遠川崎已經(jīng)成功投產(chǎn)4條機器人生產(chǎn)線。
南通中遠川崎通過船舶制造智能車間建設,實現(xiàn)了各加工系列的智能制造,保障了產(chǎn)品質(zhì)量的穩(wěn)定,縮短了加工周期,極大地提高了生產(chǎn)效率,同時,對車間的每日制造數(shù)據(jù)進行跟蹤、分析,達到工裝自動化、工藝流水化、控制智能化、管理精益化。
■先進的設計技術
南通中遠川崎所承接建造船舶都是由設計部門完成設計,包括基本設計、詳細設計(綜合設計、結(jié)構(gòu)設計、船裝設計、機裝設計、電裝設計及內(nèi)裝設計等)以及舾裝和船體生產(chǎn)工藝設計、放樣下料、數(shù)控切割數(shù)據(jù)自動生成等。經(jīng)過多年的開發(fā)、創(chuàng)新和實踐,完善的計算機集成系統(tǒng)(NACKS—CIMS),使研發(fā)、設計、采購、制造、財務、管理等部門實現(xiàn)信息化和數(shù)據(jù)共享。
■先進的生產(chǎn)過程采集與分析系統(tǒng)
南通中遠川崎在許多生產(chǎn)環(huán)節(jié)建立了數(shù)據(jù)采集和分析系統(tǒng),能充分采集制造進度、現(xiàn)場操作、質(zhì)量檢驗、安全狀況等生產(chǎn)現(xiàn)場信息,另外,還可對船東船檢的意見電子化、流程化分析處理。各塢、各船項目、各分段、各工種等的制造進度、主要工程節(jié)點、物料配送情況等生產(chǎn)現(xiàn)場信息都有專門的信息系統(tǒng)采集、整理、分析。
■柔性化的制造執(zhí)行系統(tǒng)(MES)
針對造船廠勞動強度大、工作環(huán)境惡劣等特點,南通中遠川崎采用數(shù)字化車間管理模式,以數(shù)控技術、通信技術、控制技術和網(wǎng)絡技術等先進技術為基礎,把與制造過程有關的設備(如數(shù)控切割機、工業(yè)機器人等)與上層控制計算機集成為一個系統(tǒng),從而實現(xiàn)制造設備的集中控制管理以及制造設備之間、制造設備與上層計算機之間的信息交換,控制計算機接收CAD/CAPP/CAM系統(tǒng)處理完的數(shù)據(jù),并將數(shù)據(jù)傳輸至數(shù)控切割機和工業(yè)機器人,輔之ERP系統(tǒng)的物流配送功能,實現(xiàn)了從鋼板出廠、下料、切割成品產(chǎn)出、先行小組立以及小組焊接的智能加工制造。
■企業(yè)資源計劃管理系統(tǒng)(ERP)
南通中遠川崎的ERP系統(tǒng),超越了傳統(tǒng)MRP(制造資源計劃)的概念,吸收了按時生產(chǎn)(JIT)、優(yōu)化生產(chǎn)、全面質(zhì)量管理(TQC)等先進的管理思想,極大地拓展了物流信息管理系統(tǒng)的范圍。
該系統(tǒng)與智能制造系統(tǒng)和設計系統(tǒng)高度集成,將企業(yè)的各方面資源(人力、資金、信息、物料、設備、時間、方法等)充分調(diào)配和平衡,為企業(yè)加強財務管理、提高資金運營水平、減少庫存、提高生產(chǎn)效率、降低成本等提供了強有力的工具,同時為高層管理人員經(jīng)營決策提供科學的依據(jù),有效地提高了盈利,最終全面實現(xiàn)了企業(yè)的現(xiàn)代化,提高了企業(yè)的市場競爭力。